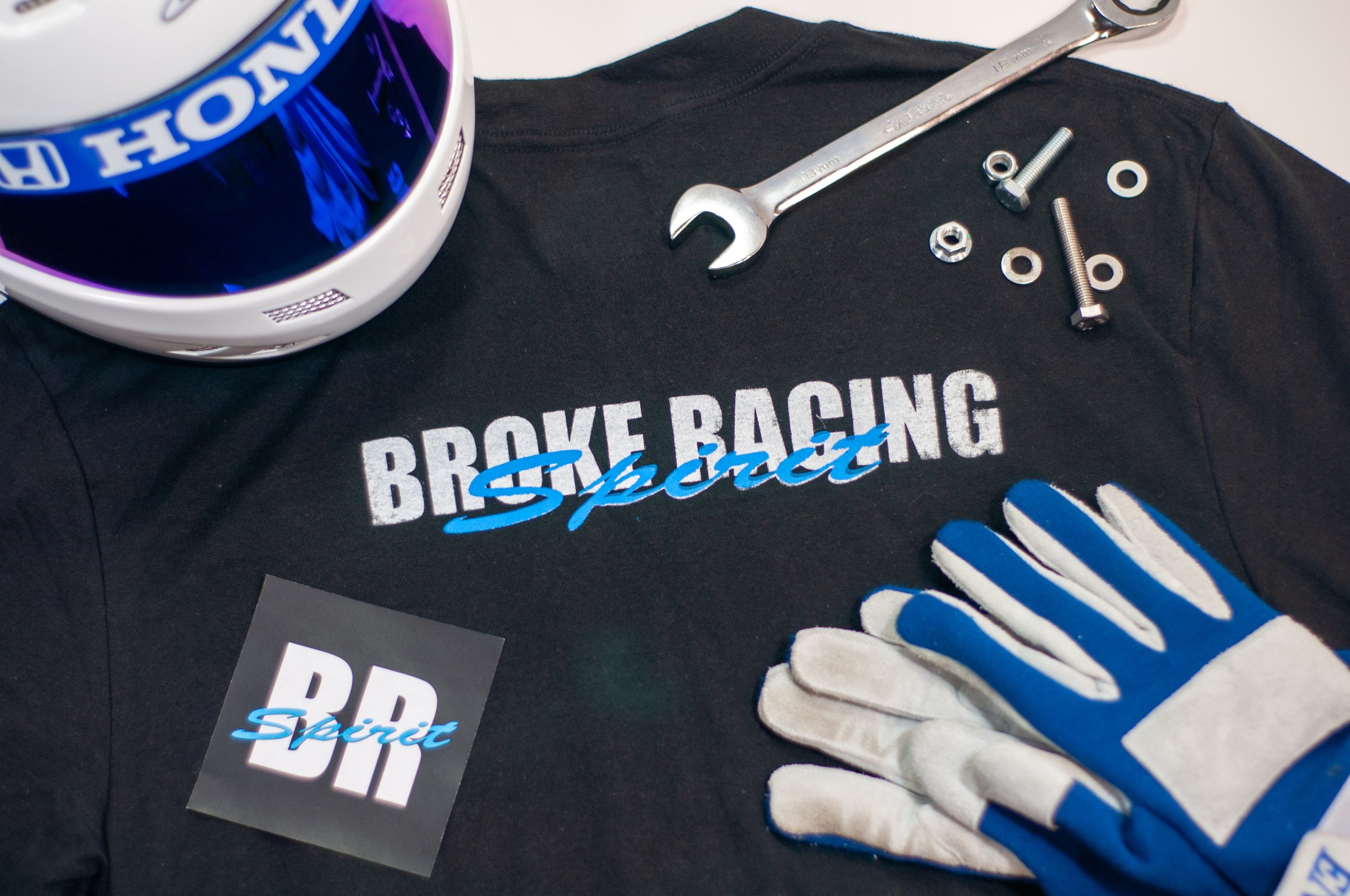
Thesis - Broke Racing Spirit Carbon Fiber
Project Brief
Design lightweight carbon fiber components for cars used in professional and amateur motorsport events to achieve higher than stock vehicle capabilities while following the vehicle’s design language.
Broke Racing Spirit is the brand through this project whose goal is to achieve industry standard results through a newly developed manufacturing process for affordable, small scale composite molding.
Through this process we are able to create low volume composite products for automotive platforms that might not have as broad of an aftermarket support for motorsport.
Why These Cars?
Rising popularity of 2nd gen Honda Fits and Mazdaspeed3’s due to the increasing affordability for car and racing enthusiasts.
Growing racing leagues specific to the Honda Fit chassis such as the Gridlife Sundae Cup and B-Spec Racing
The Mazdaspeed3 continues to be a staple platform in professional and amateur motorsports such as time attack and drag racing.
Points Of Improvement
These vehicles could benefit from carbon fiber components in several categories; dress up parts such as spoilers and mirror caps, as well as performance composites like wider fenders, brake cooling ducts and hood vents. Hood vents and brake cooling ducts are the focus as they fix some common issues with our chosen automotive platforms.
Lack of aftermarket parts to address known issues on each car (intercooler heat soak on MS3 and insufficient heat capacity on Fit brake rotors and calipers)
This is important because a lot of parts on the vehicle change their effectiveness based on temperature. Some becoming more effective as they warm up before sharply dropping off and others slowly dropping throughout.
Form Studies & Ideation

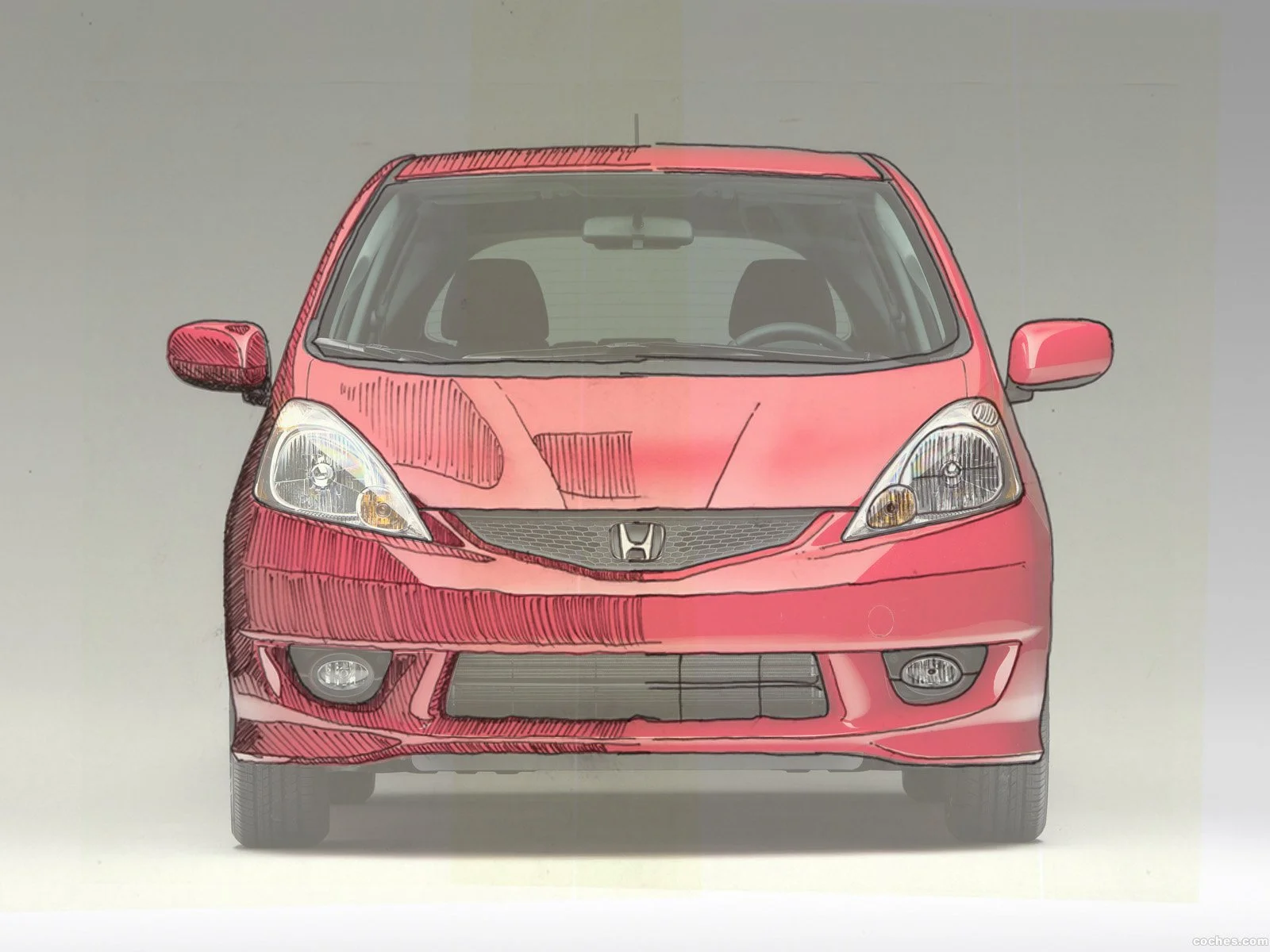
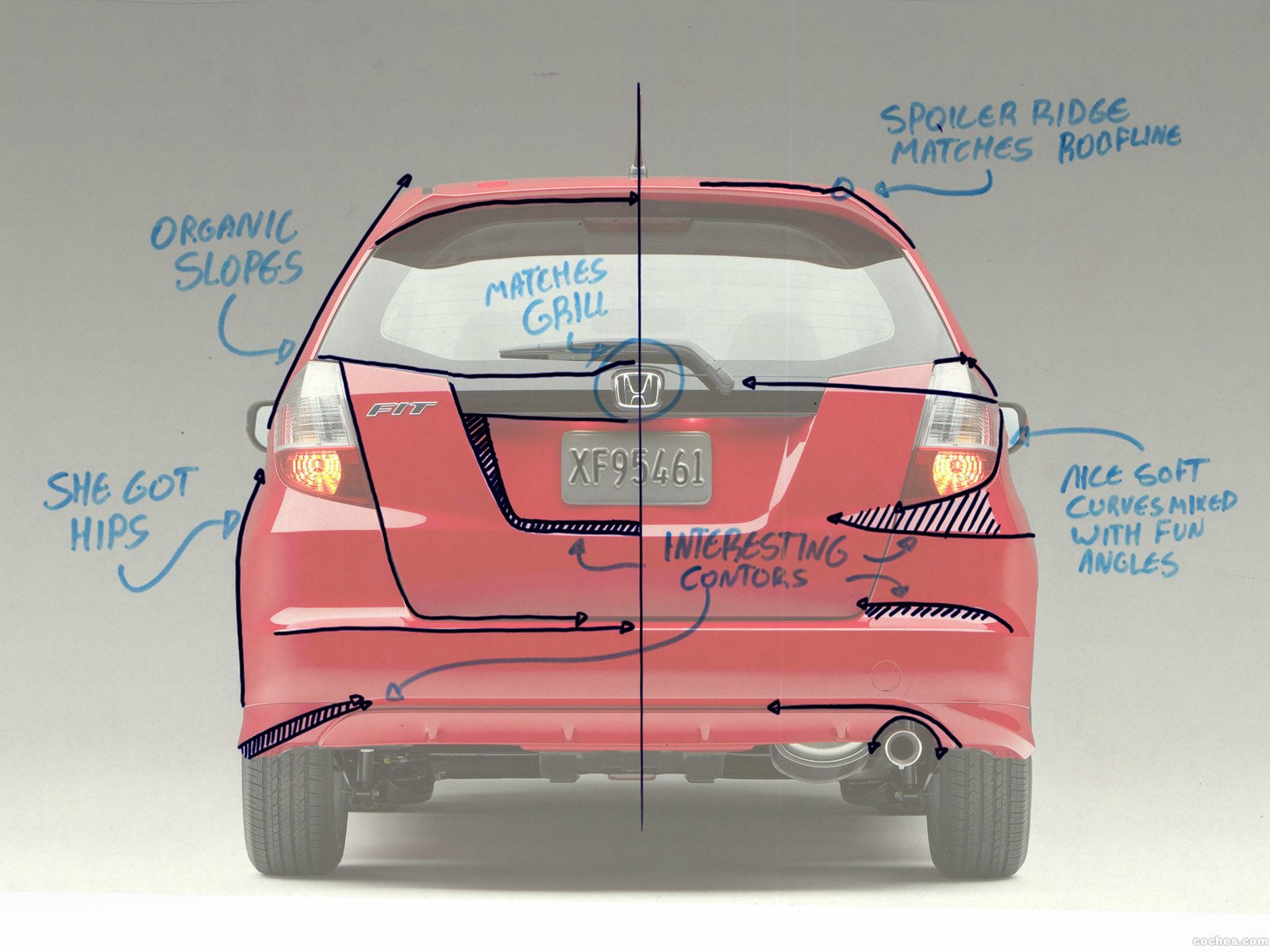
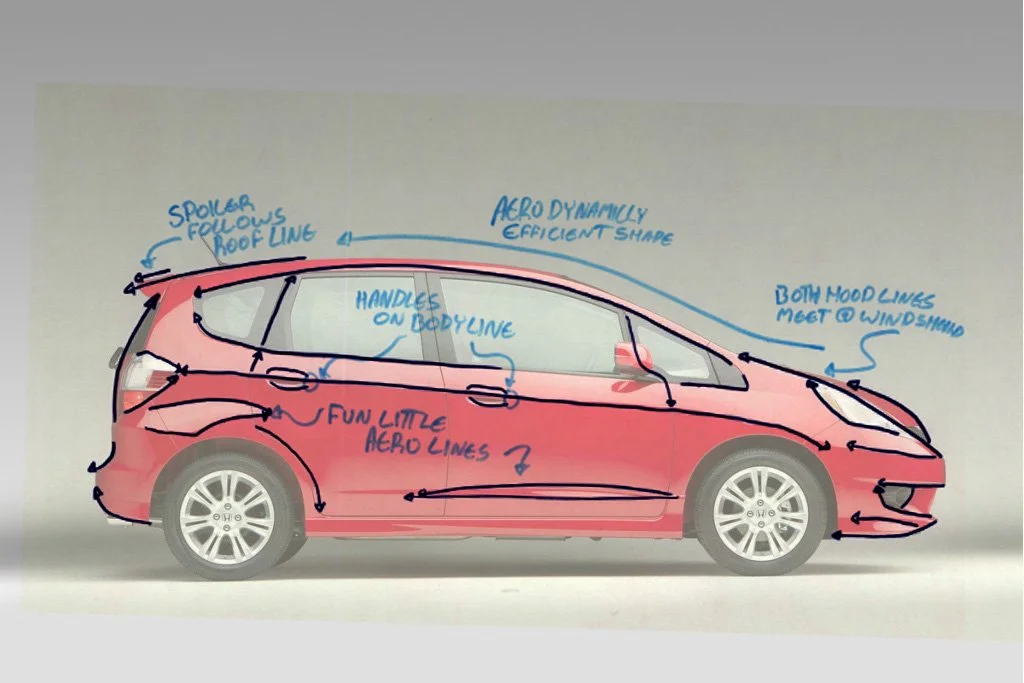
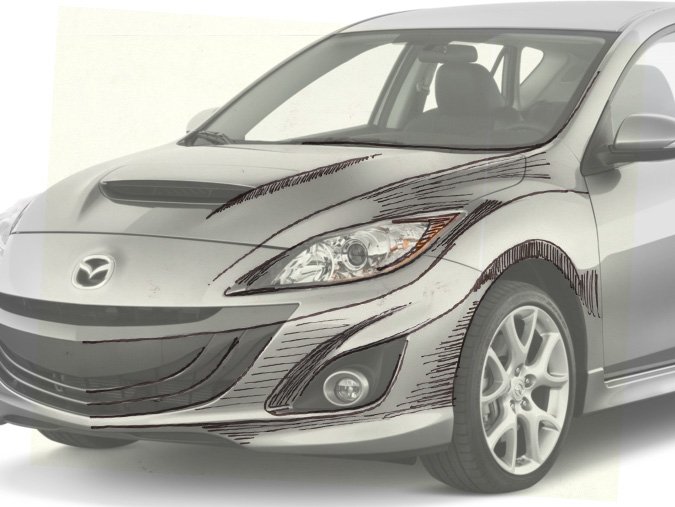
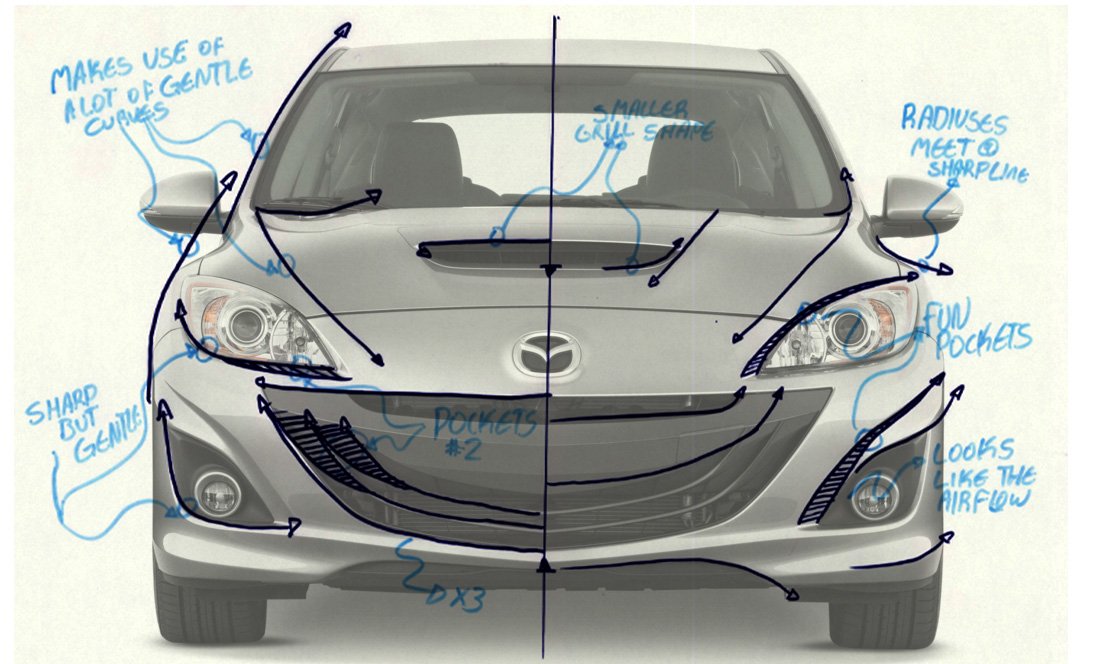
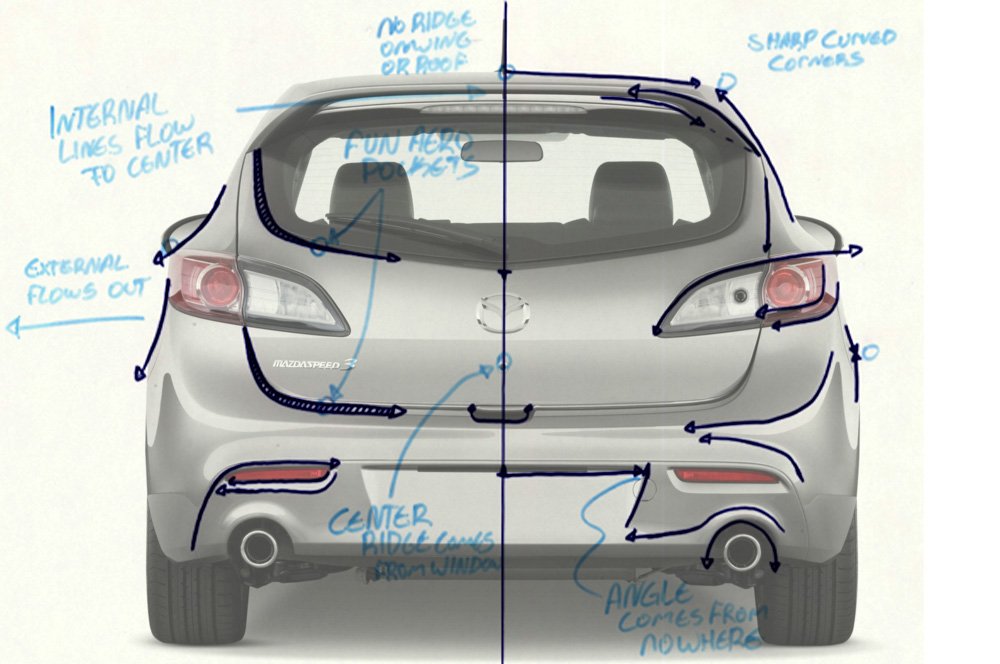
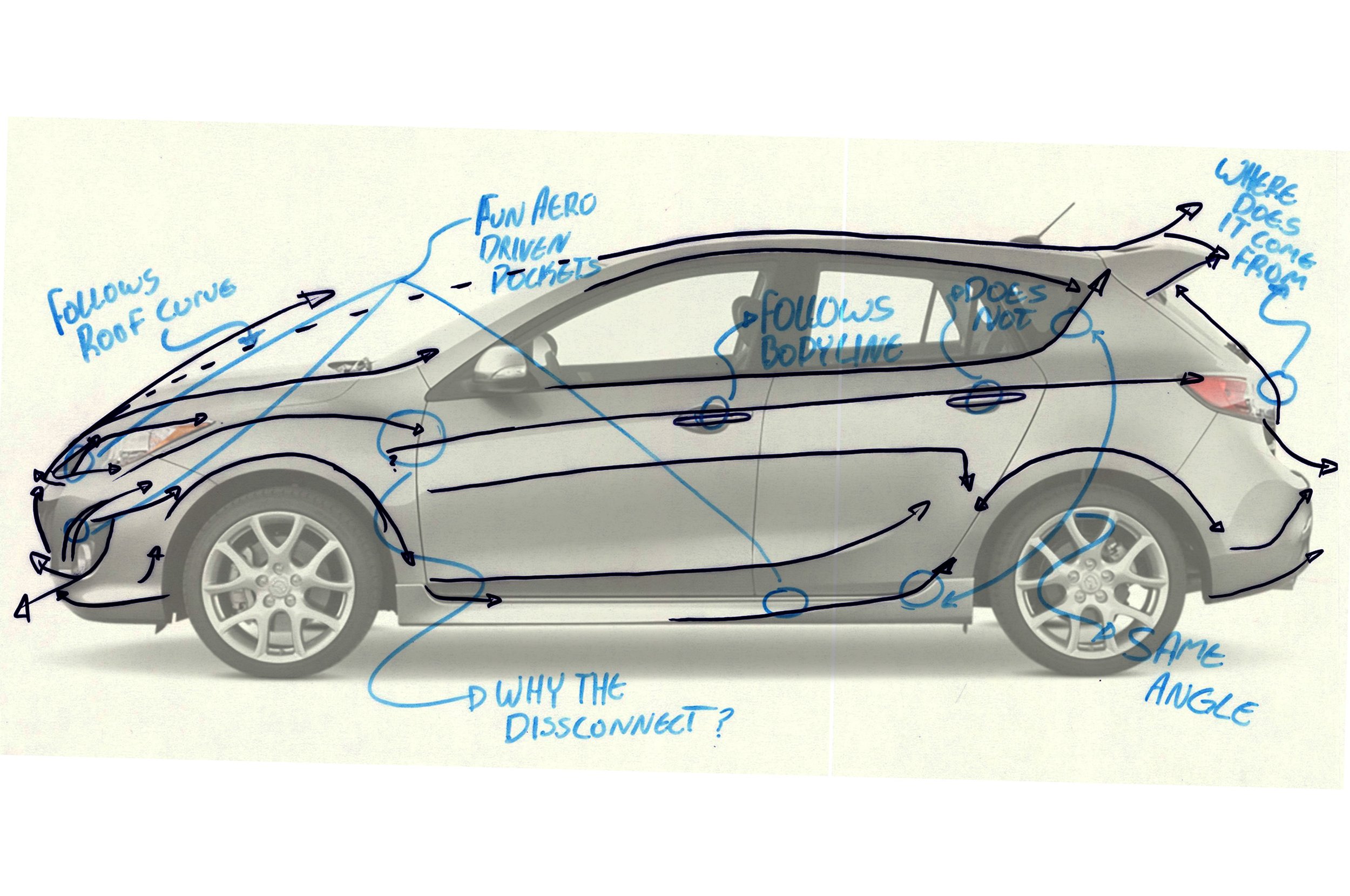
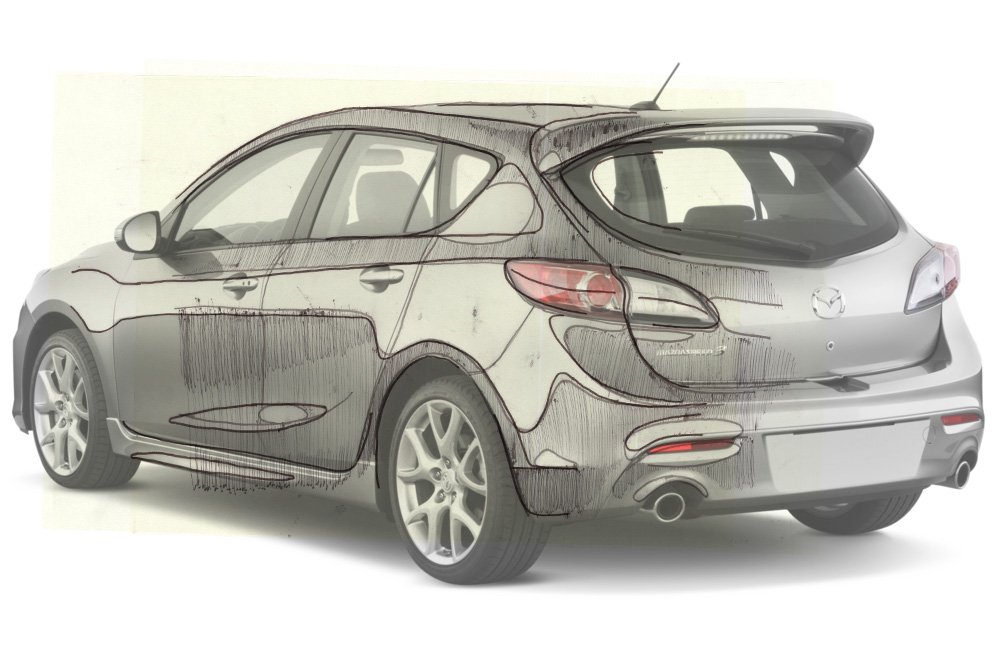
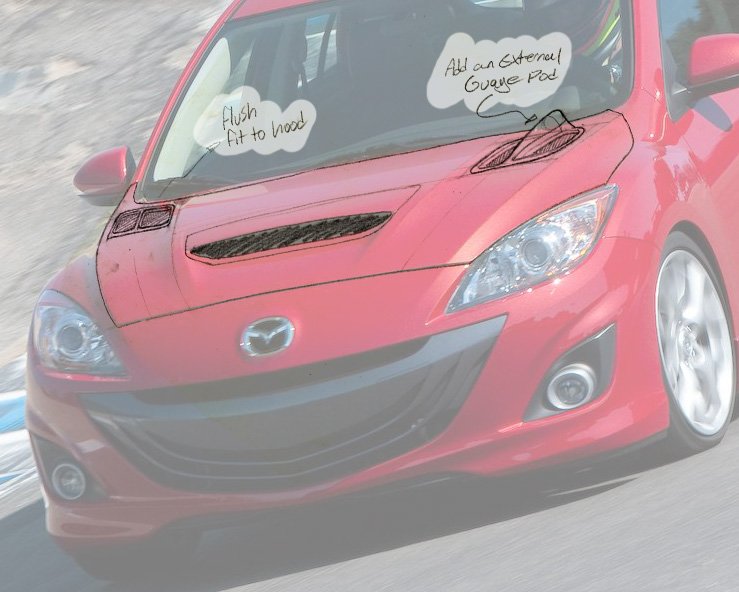
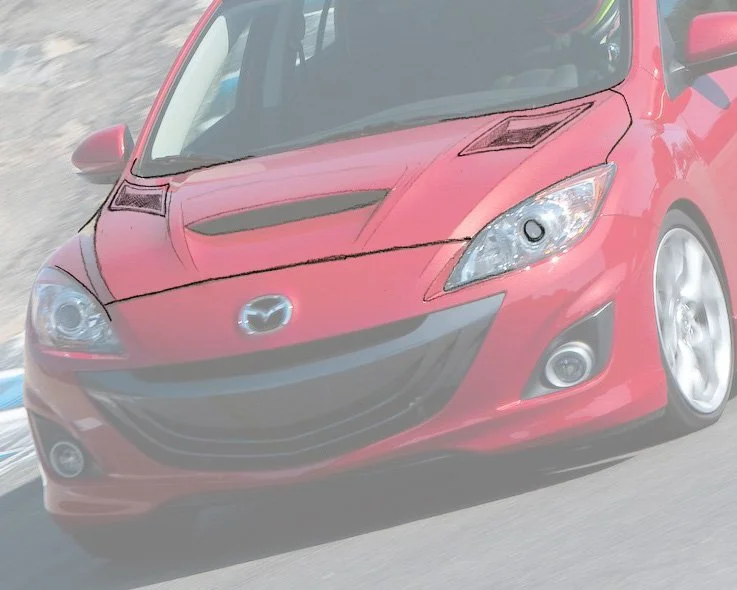
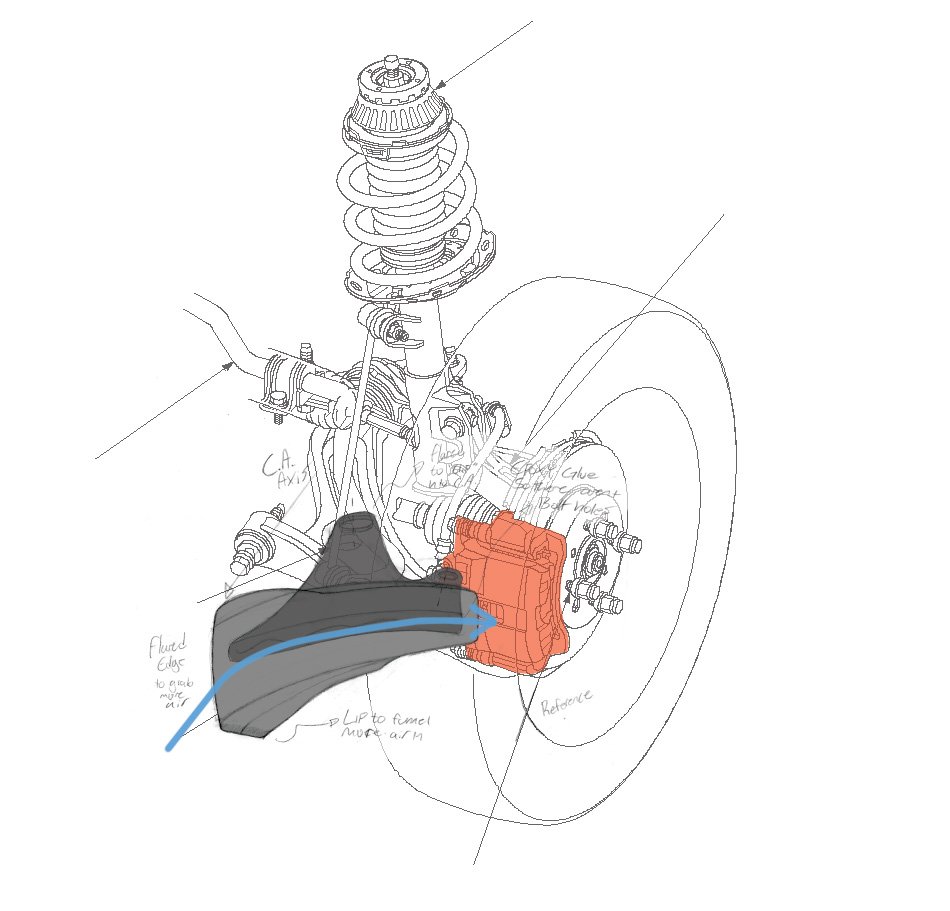
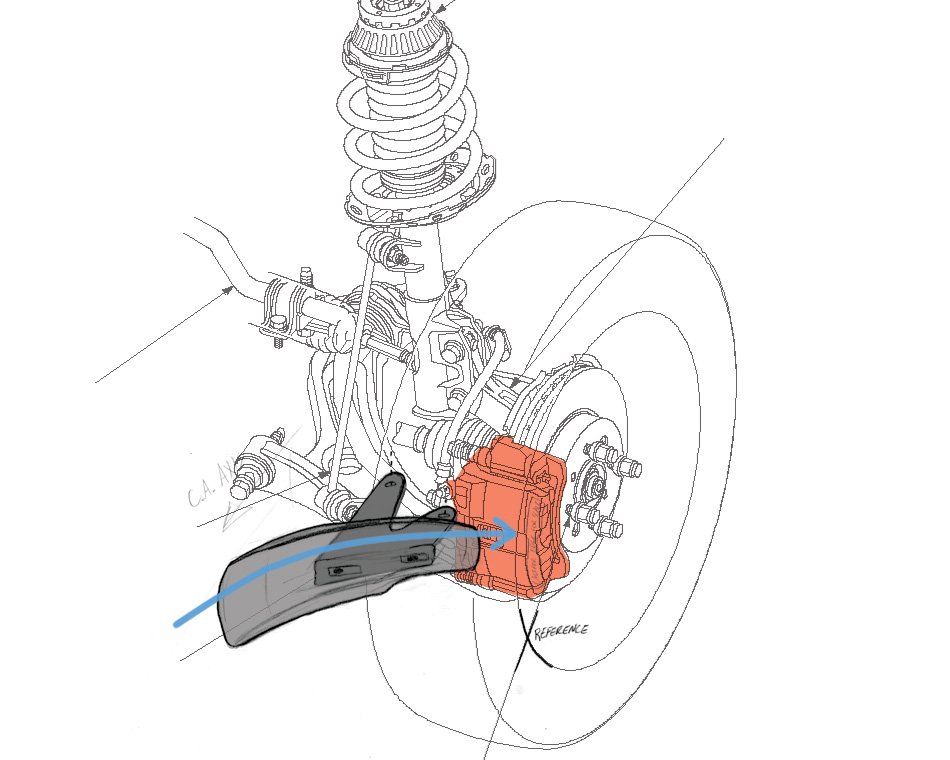
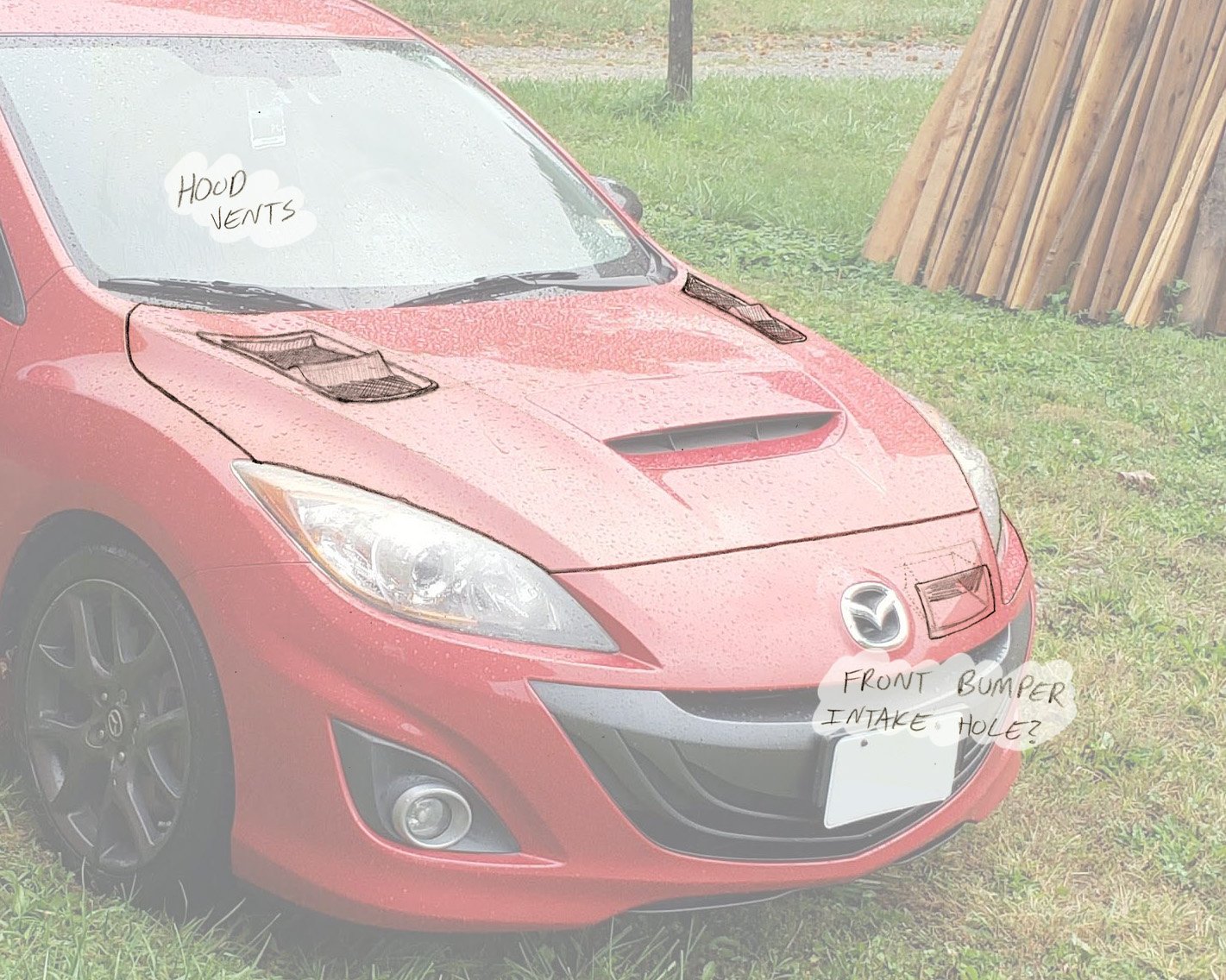
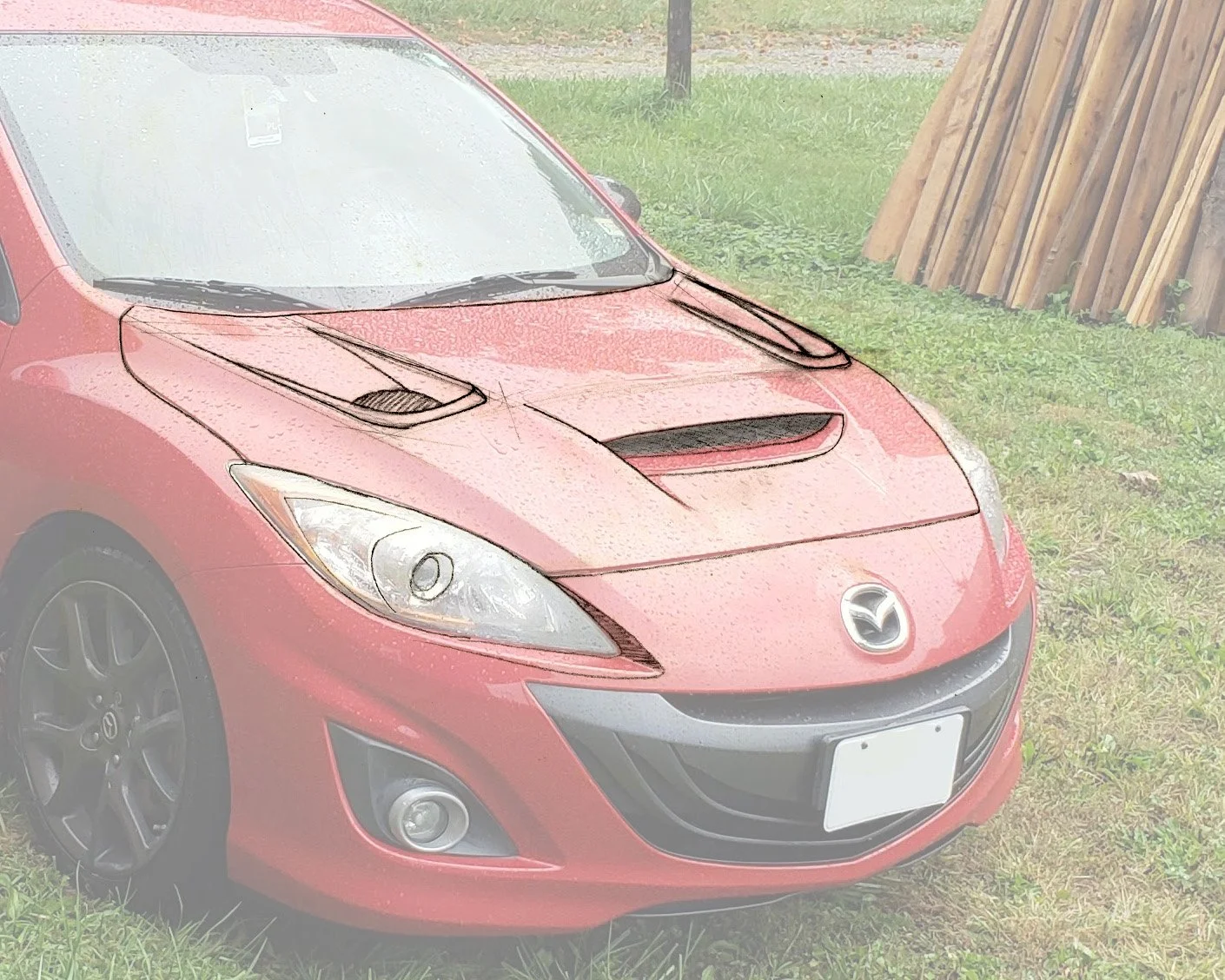
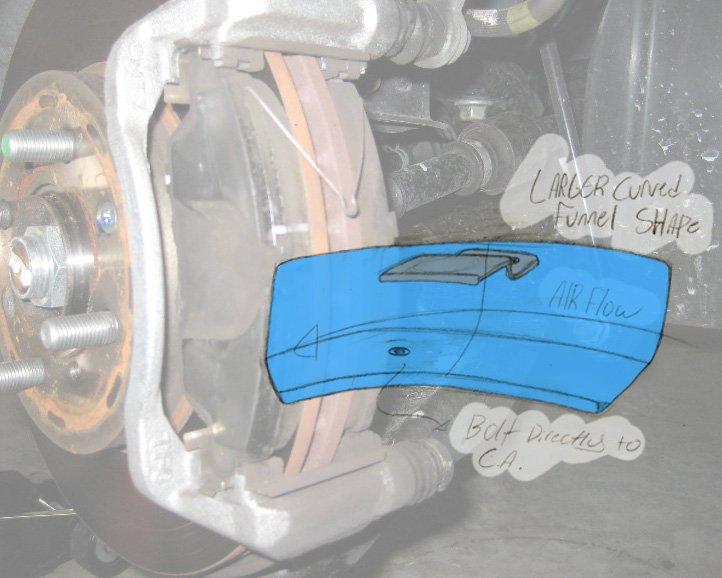
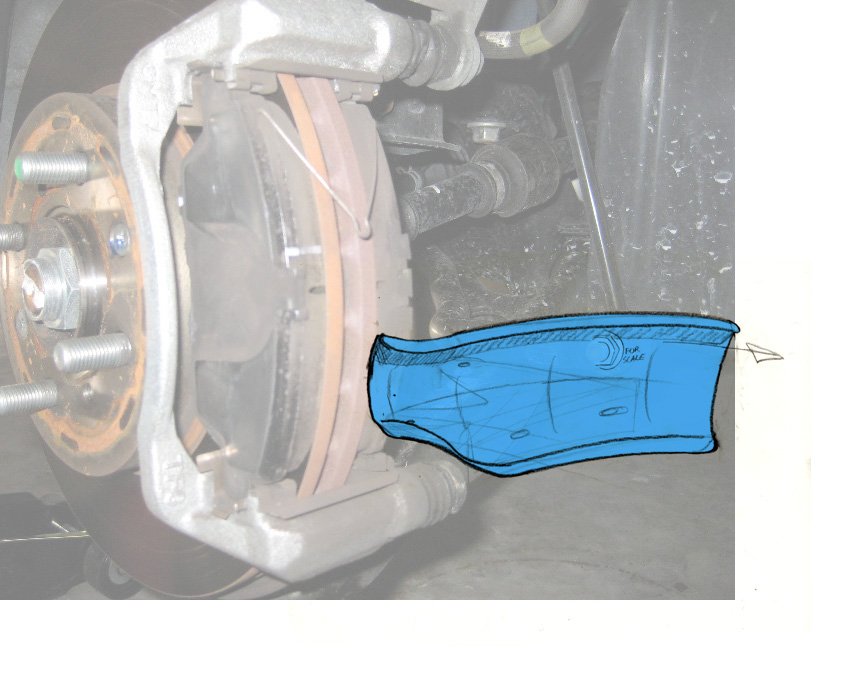
Test Fitting, Final Shots and Process
Test models were 3D printed to check fitment on the vehicle and ensure the final product would not contact the body, suspension components or wheels
The skeleton structure of the hood influenced the location and form of the vent. Test panels were 3D printed to match the curvature of the hood where the final product would be mounted.
Works like model vents were adhered to the underside of the hood to check for clearance.
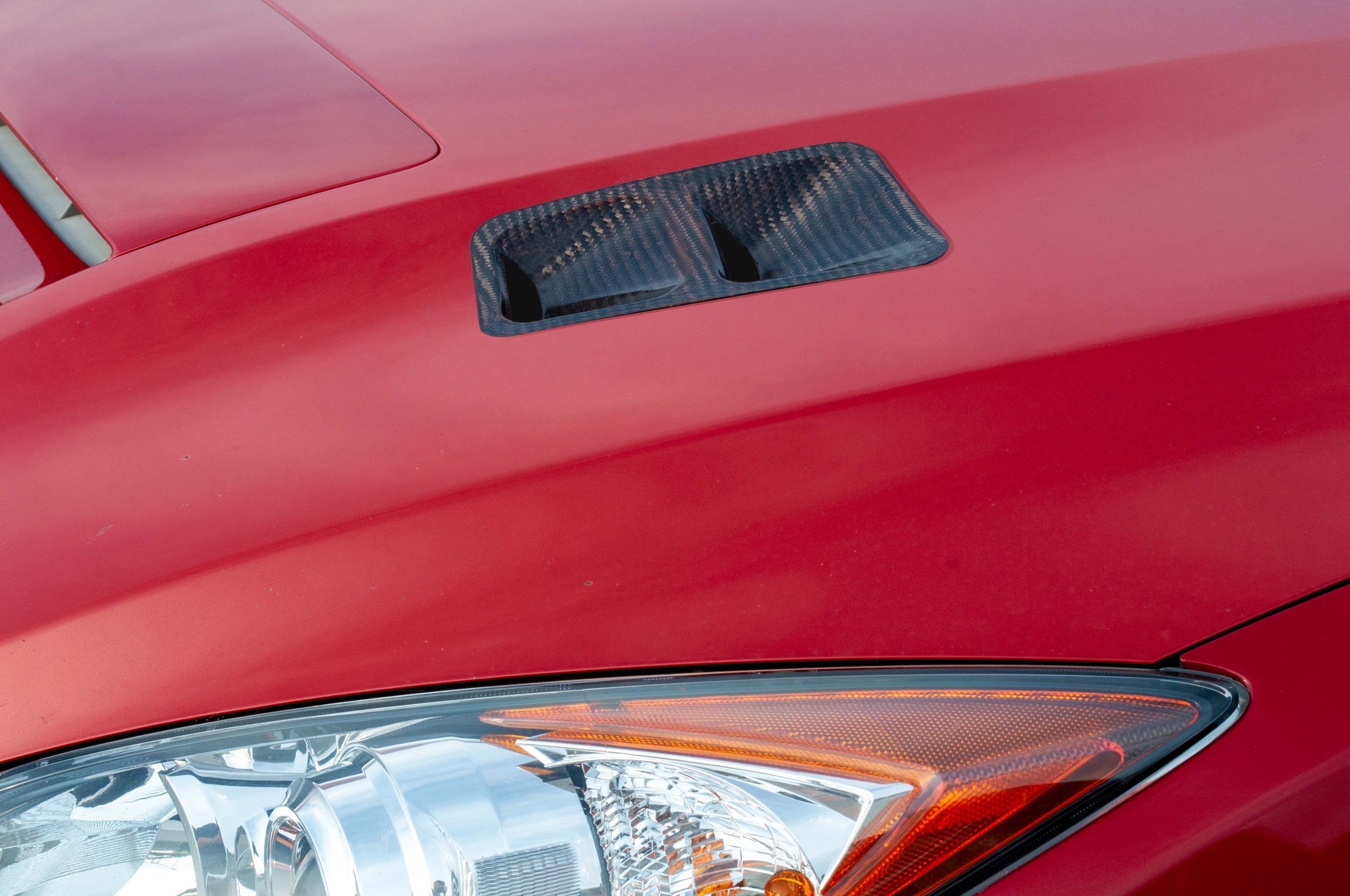
Matches the hood curvature for a flush factory look
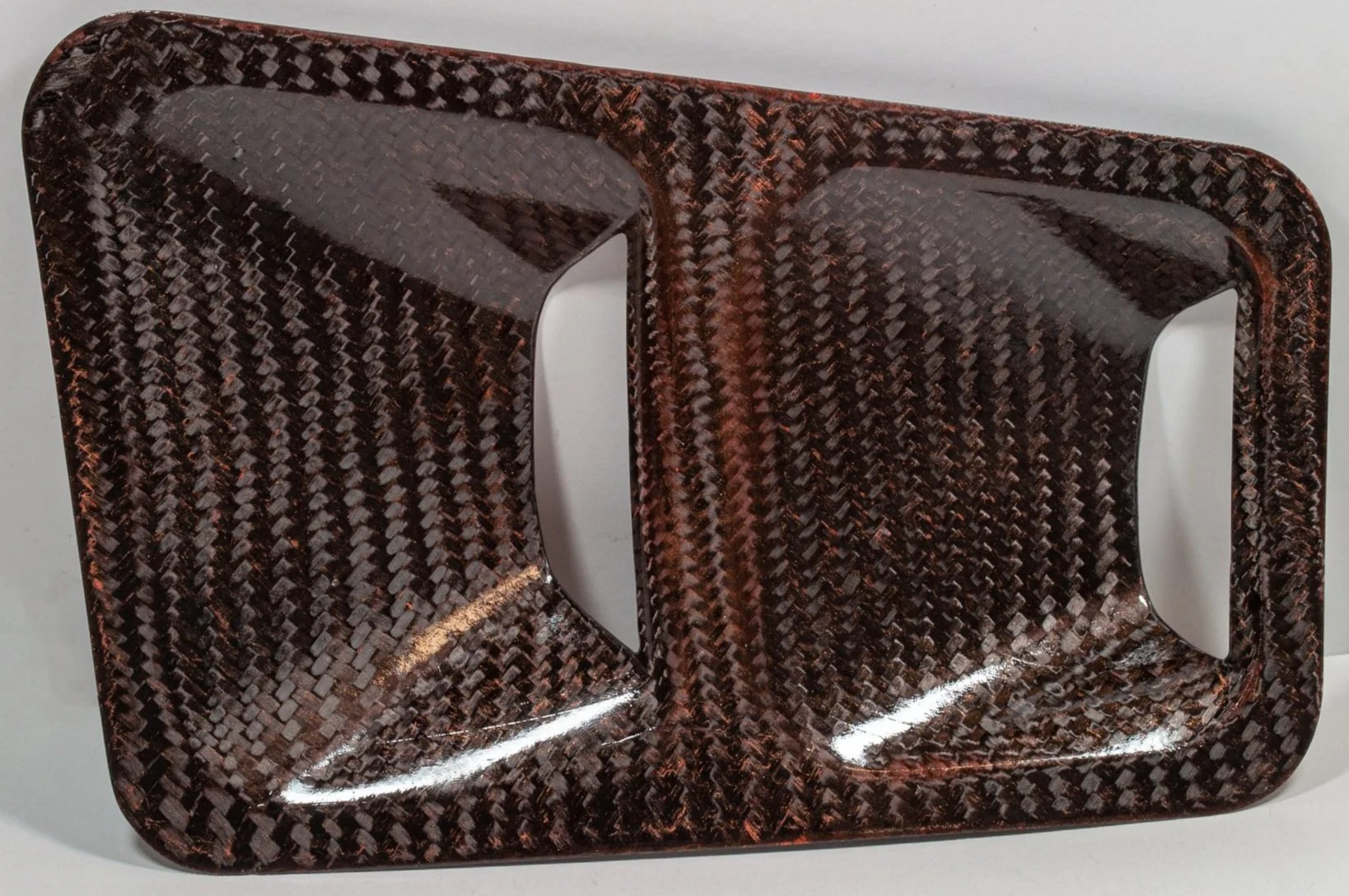
Shape influenced by the hood skeleton for ease of installation. Coated in a high strength clear coat to protect against UV degradation

Shape of openings inspired by the cars grill to match OEM design language. Double vent openings to allow more airflow out of the engine bay.
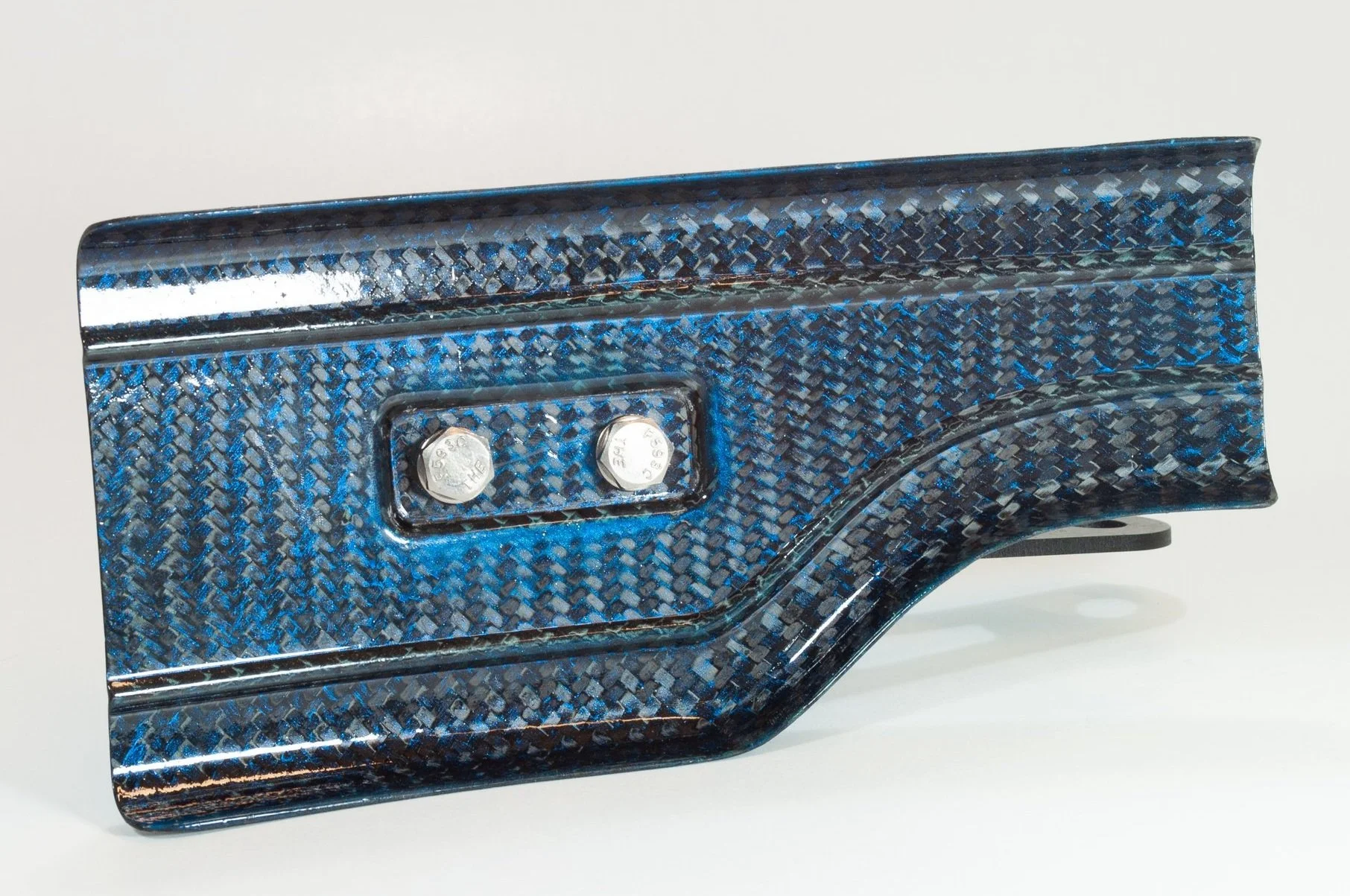
The duct curves to clear wheel barrel under full steering lock. There are ribs for torsional rigidity and a recessed pocket for hardware.
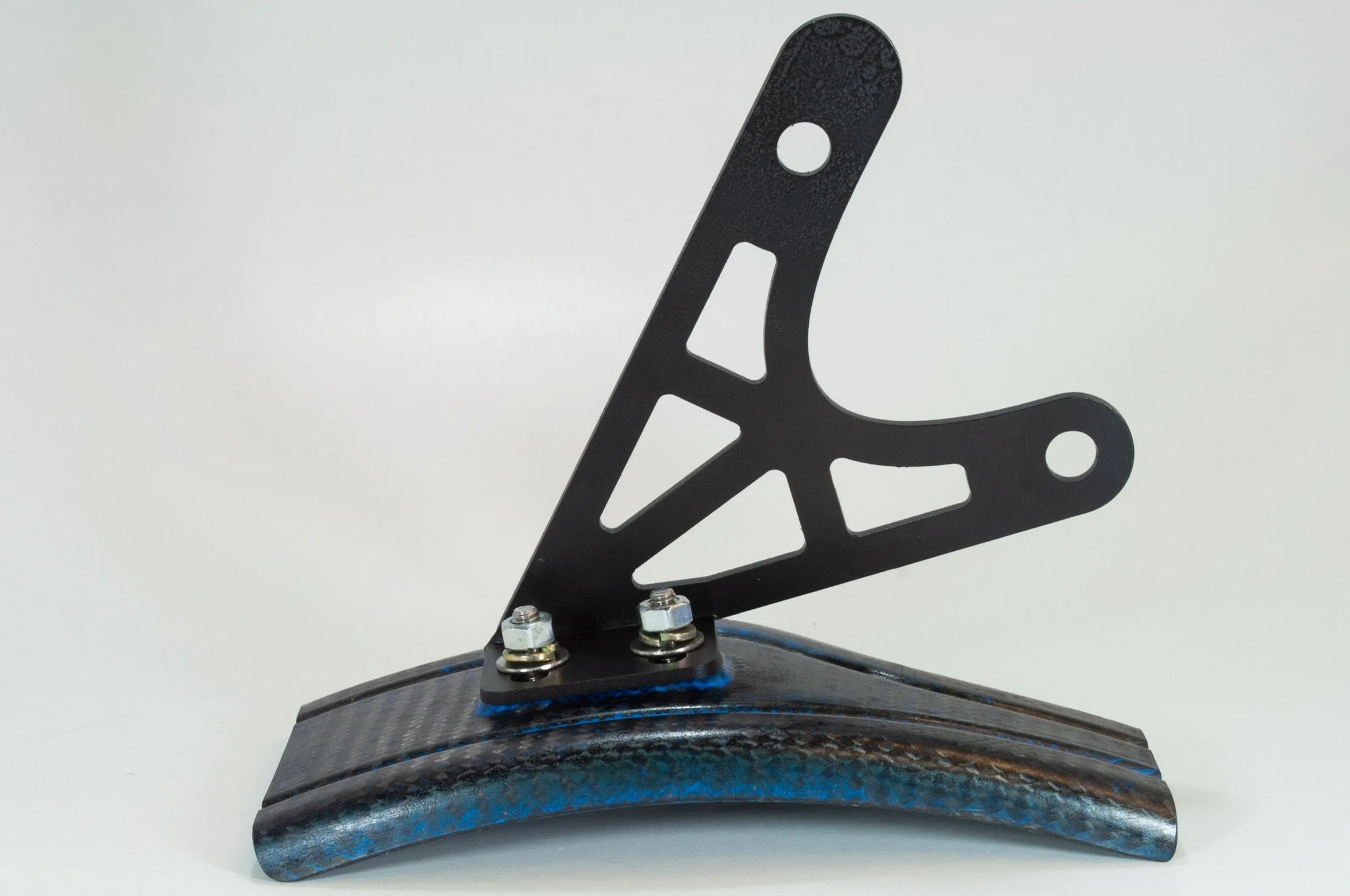
A water cut steel mounting bracket resists impacts when on track.
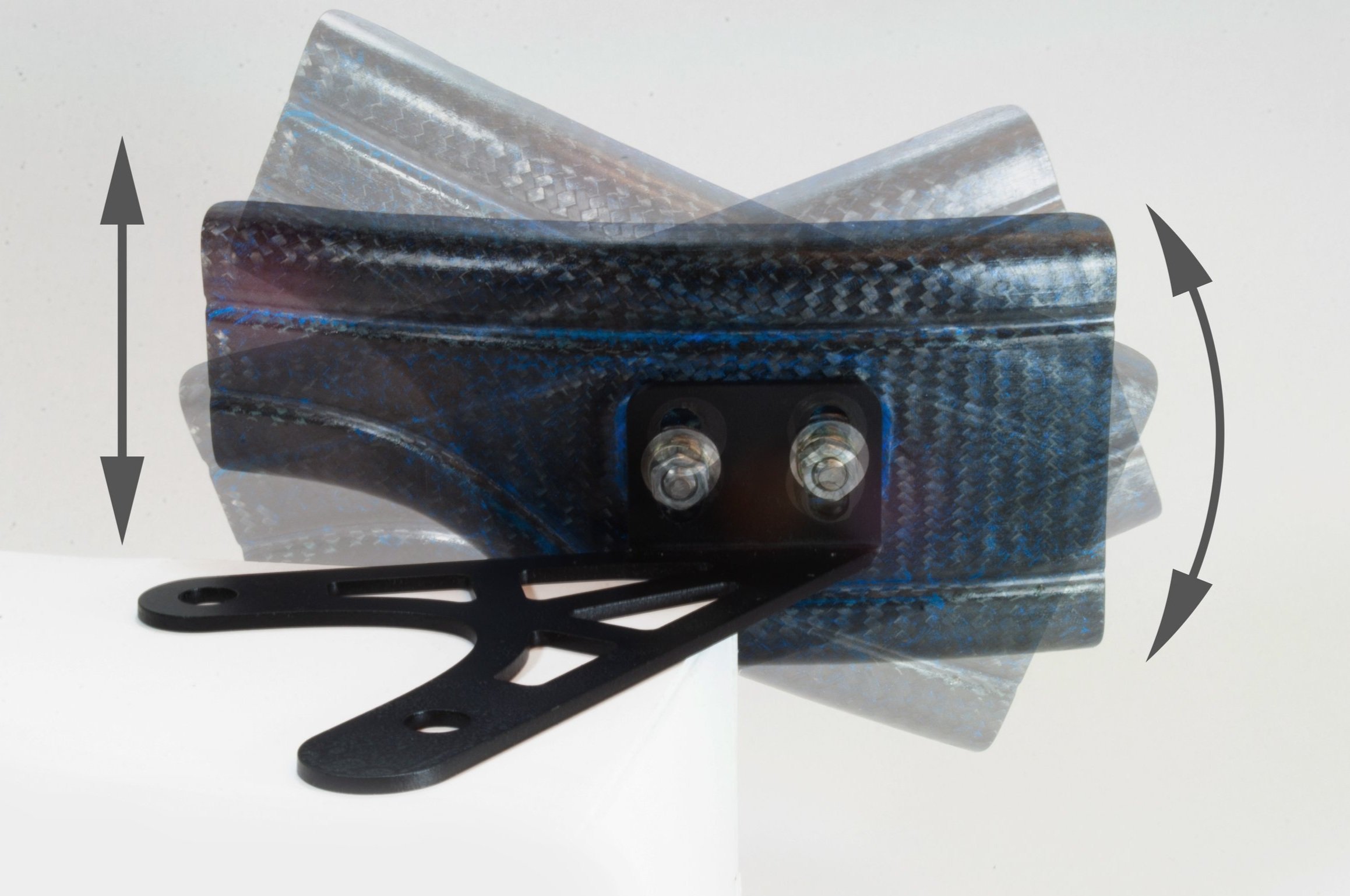
Oversized slots allow adjustability to fit different wheel and tire setups.
Molding Process
We start by creating a surface that represents the final desired composite. A mold is then split with this surface to create the male and female halves. After layup, the final composite is released and sanded to the optimal finish and clear coated.
The goal with carbon fiber is to have as little resin as possible for the best tensile strength under stress. The industry standard is 40% and with our molding method we were able to achieve 40% resin content, on par with professional production techniques.